Archify Live: Sustainable Façade Coatings & Façade Fire Testing
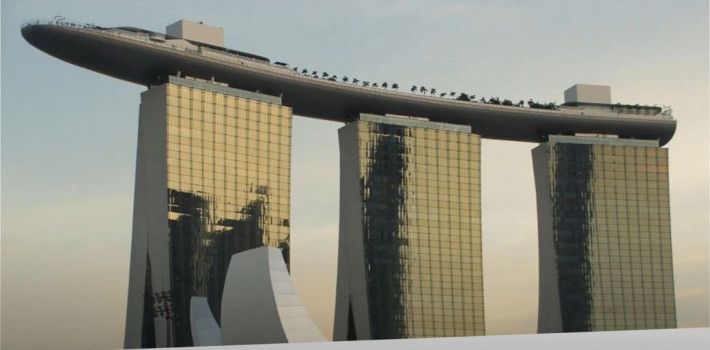
Archify Live is our web series that responds to the increasing demand for virtual learning and networking. Our latest session was held on the 10th of March 2022 and was presented by Network Architectural. Below is a transcript of the presentation.
Our presentation today is covering two topics. First is sustainability, which is based around coatings on facade panels, paint finishes and the technical advantages of some compared to others for long life. The second point is fire testing. There's a new, or newish now, Australian Standard AS 5113, which is different to everything else, but not new to the world. AS 5113 is a large scale facade system test for fire using a whole built façade, so it tells us a lot and there's a lot of good data that comes out of it that’s very interesting. There’ll be a quick video at the end to see how these things work.
Firstly, and this part will take up the bulk of this presentation, is coatings on facade finishes.
We’re going to look at high performance coatings in particular, which give long term protection against corrosion and weathering and also maintains the aesthetic integrity of the facade through the colour and gloss retention of the finish.
If we talk about protection from degradation with metal facade panels, obviously corrosion is a big problem, even for alloys. Using a performance coating is critical to the sustainable life of the building. We’re talking about buildings here, but think of the importance of this when you look at the aerospace industry. For example, having high performance coatings on their airplanes is critical. So paint and coating performance is very important to the end use of the product, often it’s over looked.
We don't seem to see the importance of it, certainly it's not reflected in the depth of specification wording out there in the marketplace. When you're considering this, you have to think about where the coating is going, what the application is, and where the site of the building is. The chemistry involved to create this coatings vary quite a bit.
Think about what sort of properties that you're going to need. For example, if it's a high rise structure, then weatherability is important to avoid costly repainting and height access equipment. You want to avoid that, as do the aircraft people. They don’t want to park an A380 aircraft, put it in the hangar and repaint it for a week. Before COVID they were paranoid about keeping that sort of infrastructure moving. Starting with your high rises, you don't want to repaint those things in 20 years, even that's a stretch. You can avoid that by good selection in the first place.
The other important thing that we're going to cover today is warranty once again, which is often overlooked. There's a lot of warranties out there with cleaning clauses in them, which I see is a loophole. That's something to be aware of as an architect and a specifier to avoid cleaning clauses. UV performance is extremely important to avoid sunlight damage. Equally important is to prevent corrosion to the underlying substrate.
So here, if you look at the top of this slide, we have two of the most widely used fluoropolymer coatings in our marketplace. On the left, there's PVDF, which I know a lot of you are familiar with, because I see a lot of generic cut and paste specification clauses mentioning PVDF. That was introduced about 50 years ago as a technology. But since then, it's evolved to a new generation of fluoropolymer. that's called FEVE, that came along about 35 years ago and has a better compositional chemistry, which resulted in superior cross linking during the curing of the coating. It delivers on performance, we'll have a look at that.
The chemistry is vital to the performance. What we're looking at here is the structure of FEVE. What's important about this diagram to keep in mind is that the vinyl ether (the V part of the FEV), represented by the green components, are not very weatherable. If you had a coating system that just had this component, it would not last very long.
When you have alternating copolymer with fluoroethylene right next to those vinyl ethers in regular and repeating patterns, as you see in the diagram, you end up with something that weathers very well, superiorly to the market. It’s a whole new step forward beyond PVDF. So you might ask the question, why is there VE in the first place? It allows this chemistry formula to have great solubility with common solvents. If it’s applied wet out of a bucket, which they do with bridges, the old 100 year old method of application, it allows a superior coating on without having to cure it at room temperatures. And it's environmentally friendly, because it's easily soluble.
Now we're concentrating on FEVE, this newer technology. I'd love to see you guys upgrade your spec clauses from PVDF to FEVE, because it'll give you outstanding benefits. It’s number one for UV protection performance, better than PVDF. I'll show you some evidence to that soon. This means the material will not degrade significantly from UV light. Degradation of the paint, as you know, is when the molecules break down and you get things like chalking and fading. If you're looking at an example of a car headlight though the clear plastic, when that plastic degrades, it frosts up. That’s actually the molecules coming off and breaking down. That’s what is called cleaving which, when you look at it in the macro sense, is micro cracking, and that contributes to gloss loss on your facade panels. When this process happens, if it's not UV resilient, you'll get that chalking and then the loss of gloss. When you put your hand over an old white painted surface and you get it on your hand, that's chalking that has wiped off. UV protection is extremely essential, that’s why fluoropolymers are used, fluoropolymers being those two categories: the old PVDF and the newer FEVE. Both are very good, but FEVE is better, it's a new generation beyond what we've had for 50 years.
So FEVE chemistry is the best, it does not absorb any amount of UV light. That molecule structure that I showed you earlier is a bit like sunscreen on the pigment of the colour of your building. It’s stronger in chemical formula, so that the UV can't work through and degrade the colour through it. It’s the sunscreen on your building in a simplistic sense.
Now, the benefits of FEVE for architecture. We don't do aircraft, we don't do bridges, we're looking at buildings and that picture there is Queensland Children's Hospital with an Alpolic FEVE paint finish on it, the fire safe grade, which has been fire safe for 20 years. Now, talking about specifications, there is a code. Always look for the spec test standard AAMA 2605, it is a good standard to specify. It’s an American Standard. Why not Australian Standard? Because there is none, and there’s no European either. Worldwide, everyone goes to American Standard. The Americans put a fair bit of energy into creating standards on coating finishes, and this is a good one to latch on to. This benchmark, however, allows for 50% gloss loss over 10 years, so this is not a great benchmark. Looking at that hospital on the on the screen now and you wouldn't want that to lose its 50% of its gloss in 10 years. AAMA 2605, which I do see in a lot of specification, will not protect your client from a substandard performance.
But there's good news, I have some more information for you on a performance based specification, which will give you a rock-solid, watertight specification to deliver on performance. The aesthetics is another bonus, FEVE gives you optically clear finishes. So when you use bright, crisp primary colours, or crisp secondary colours, you get a beautiful sharp finish on your building. You’ll get a wide range of gloss levels, which PVDF doesn't do. If you want a super matte, which is popular at the moment, we have G10, which means gloss level is at 10%. So if you've got a colour, for example silver metallic G10, the gloss level is 10%, and that's a super matte. If you have a silver metallic G30, the commodity finish out there, that's a satin finish. If you have a silver metallic G80 specified, you've gone for a high gloss and we sell that in our Alpolic for Toyota dealerships. G80 is usually preferred in white, and I also spin that often in a lot of buildings too where architects or interior designers want a higher gloss aluminium panel finish in white. That’s your different gloss levels, FEVE does that over PVDF.
I talked before about the crisp purity of delivery of your colour with FEVE. The reason for that is that FEVE optically is clear, as you can see on the slide. There's two test tubes, one is filled with FEVE, clear, and the other is with PVDF. You can see PVDF by its nature is milky. It’s not going to milk out your total colour as we see on that slide with the rainbow colour put behind those test tubes, but what it does is, when you put in a paint finish, it takes the edge out of the colour. FEV gives you a crisp, sharp colour, and that's the evidence there.
Now, performance testing is a great area, because it's so interesting.
In performance tests, they test both for aesthetics and for function. A lot of this is done in the US, as I mentioned earlier, because they really dug their teeth into this area in the data. They do it often through accelerated testing, because you might not want to wait 30 years to get a result. But they do both, they do accelerated and real time testing.
Ideally, you want these tests to be real time because you can't beat real time versus lab, simulated or accelerated, so they do both. They do a lot of this testing in real time in South Florida. The reason that's chosen is that it has a climate similar to Far North Queensland or Darwin because it's humid, and it's hot, and it has a high UV, and that's what they want. That's the things that paint finishes hate, that's what causes degradation so quickly.
So that is why they do it in South Florida. To develop by accelerated testing, they benchmark the real time test result trial with an accelerated test to duplicate the result. And not surprisingly, they're not guessing with accelerated results. FEVE has been around long enough to compare to real time, and that early accelerated testing did ring true versus the real time tests, the data matched.
This particular test is for accelerated weathering using what’s known as a QUV to test, using energy bulbs. They're looking at gloss retention here. Remember, gloss retention is a measure of degradation. As I said before about the car headlight, when the cars eight years old typically the headlight lens fogs up, and that's degradation. Gloss retention will tell the people testing it how it degrades, that's what they look at here and is a good indicator to the percentage of the value.
There's some data for FEVE at the top, it started at 100%. After accelerated exposure through high UV for 6000 hours, it’s sitting at about 94%. Have a look at those other paint finishes, acrylic particularly, just woeful. So as I said, you want a high quality performance paint for these large architectural structures.
This one here is looking at another chamber where artificial bulbs are used for the UV light. This one is a little more representative to what sunlight exposure is and you can see a comparison graph. What this does is it mirrors and tracks the sun as well, and some of these units also spray salt or water onto the panel or the paint finish. On the left you see, for the first time on my slides in any case, the data here between FEVE and PVDF. I said at the beginning about fluoropolymers, both categories are great, very good performance. But there is a better one now, and that's FEVE. You can see from that data, how much it beats it by, about 10% over 4000 hours. You know when you're looking over the span of a large commercial building, for an architectural finish, you don't want to get height access equipment and you don't want to repaint it. That’s going to make a fair difference on the aesthetics of this building at the 15 year, 20 year mark, more so even at the 25 year mark. This impacts sustainability too, to avoid those recoatings.
This is called a Xexon Arc Test, another chamber test, with a different set of bulbs this case. This one has the wet cycle on so they spray water and salt on this. This is in Arizona in this picture. That's a dry climate, so they introduce rain and humidity by spraying it at the same time artificially, but also using the sun and mirrors to track the sun through the day. They spray it with water at night to avoid thermal shock. You can imagine the heat coming off those mirrors because they have approximately eight suns worth reflecting on it with mirrors. So that's accelerating times eight, but it's in Arizona, so you're avoiding cloud cover; it's full on UV. They put the water on at night because it would probably sizzle if you did it through the day, and that give him a wrong reading on real life application. Once again, there's FEVE and PVDF, still reflecting different apparatus, different test process, same data. This is good news, because we haven't got conflicting data it's selling a solid story on what we can expect on these paint finishes.
Here is real life weathering for the first time. South Florida, as I said before, is a good extreme environment. It gives it the sun, gives it the humidity and the rain on the one here. Here we have two sets of data running here for real time weathering. This is just FEVE Measurements here, a clear and a yellow, we only use the clear, but that's more data on it.
This is real life data from samples of real life results. This one is South Florida and you can see there on the left are the painted panels. At the top, towards the 80%-90% height of these columns, you see a black line, unexposed and exposed. With unexposed, it's covered fully and blacked out during this exposure period. So there is no UV penetration to that site, giving you the original colour. from that, you can see here the colour degradation and gloss level. In the case of red, you buy a red car and you can expect it to powder off very, very quickly. If you use red and FEVE, your customer or client is in a good place. They’re going to have a Pillar-box Red feature component on their high rise building in the CBD, still looking crisp and red 20 years on. If it's FEVE, that's the difference. Looking at the polyester and what a mess. In the middle of that we see a comparison between FEVE and PVDF. PVDF is in the middle in dark heritage green. PVDF is doing fine, but your FEVE is doing better. Once again, a comparison of FEVE and PVDF in that ochre, yellow gold colour, FEVE is looking better. Identical, in fact, to its original, same as that the dark FEVE.
This is our real time weathering testing here, we're looking at an offshore oil rig. They're measuring the thicknesses, starting with 25 microns, and as it degrades, the layer thickness degrades. Here FEVE goes from 25 down to 21, still plenty of finish, coating protection and corrosion protection for your structure. This is on an oil rig out in the sea, lots of metal and harsh environments for 16 years.
I talked earlier about specifications. The Americans have the AAMA 2605, but there’s even worse standards for other areas. For a good specification, you want to be looking at this much data, it's worth it. You can still cut and paste, there’s no more work on this, I'll give you a copy of this. You can see this goes way beyond just that one American test. There's lots of standards in it. The reason why you do this is that when you get a project, let's say you use an inferior paint, or they sneak in a Chinese paint or finish, and it's dodgy and fails, you want a warranty that actually references some data, so you have a fair umpire to call. I've seen warranties out there from big brands in my industry that use weasel words such as “should maintain reasonable gloss levels”, “reasonable colour retention”, how are you going to argue that with someone about the word reasonable? Well, that spec I showed you before, no arguments there.
You actually have data and test measurements that you can send a sample off to a lab and have the evidence to fight a good fight on it, and they’ll just buckle and deliver against it. Put it in your spec, is what I'm saying.
Avoid suppliers that have made cleaning clauses for your customer, your building owner, or your client to wash their building down twice a year, three times a year, or even once a year. That's an outrageous cost. It’s a loophole, so put in a clause in your specification, which I'll send you, that states there's not to be any cleaning clauses through the panel brand.
That's the cost of your cleaning. It works at about nine bucks a square metre, it'll cost your client zero with Alpolic. If you look at costs to the right, depending on how many clauses, if it's twice a year they're looking at $36,000 per annum for 2000 metres, and that's a big amount. that's about an average for an average size commercial building with aluminium panels. Don’t put your client in that place, look for that sort of thing.
Look for a warranty, read the warranty to make sure it’s a full coverage warranty, which Mitsubishi gives. The other guys only give you the material so they're only covering a third of it.
Here's some failures, I live and work in Brisbane. These are local, I don’t have to ask people to take photos, and they are there to see. there's some angry building owners out here, and I'd be I'd be pretty angry at my consultant if this is my building after seven years in West End, which is on the perimeter shoulder of the CBD.
Once again this is Chinese panel, this is seven years and it's disgraceful.
This is a Queensland government building, so don't think that only private consumers are vulnerable to this, this is the big end of town. They specified a quality product, the builder swapped it out to a Chinese panel and it's near breaking surf at Maroochydore. Now they’ve got a high rise government office tower and it's corroding. Its alloy, but it still corrodes, its rubbish. Rubbish film, rubbish paint that lets the corrosion in under it, and that's just junk.
This, on the other hand, is 20 years old, Q1 at Surfers Paradise. That's Alpolic, made in Japan, reputable brand, Mitsubishi. 20 years, no corrosion, no chalking, no fading, no colour loss. A good brand. A big difference, really is.
This another thing you want to avoid guys, this is solid aluminium out there at the moment with tiger stripes. This is because it’s a Chinese brand, as all of them are pretty much, and because of the way they apply it. That’s unacceptable, if you bought a Mazda car and the bonnet looked like that, would you not take it back to the dealer immediately? I would, and I know you would. Think about your building owner, why is that acceptable? It's just not.
Same as that, see the colour variation through this. It's another building in Brisbane. That's a solid aluminium and you can see the shading, which would be just unacceptable for a good brand like Mitsubishi. Once again, if you bought your new car from here, would you tolerate the front door to the back door with that colour shift? You'd send it straight back to the dealer. Well, the manufacturer of this panel told the building owner, architect and the fabricator that that's within their factory tolerance. Well, aren't we happy for them? As long as the factory is happy, we’re not thinking about the architect or the end user. Strong specification needs to be applied to discipline this sort of stuff.
Once again, another car dealership Southport, look at those tiger strikes. They put all their trust in a consultant to manage this for them through specification, tender and build.
To avoid those tiger stripes with FEVE, I've highlighted a clause there which is in my standard spec, it needs to be a die coated process.
Manage it through a specification by telling them to not do a roller coat, which you see here on the left, because you don't want tiger stripes on the paint finish.
I'm going to talk about AS 5113. This is a full scale fire test, it's so good. Australia implemented this and released it based on a European test BS 8414. Why? because it's full scale. This is like building the whole facade and lighting it up. Whereas the simplistic non-combustible test, which still has its place and that's your first step reviewing products, goes component only. You have no idea how it's going to perform in your build. In this test the whole façade is lit up, the insulation, sub-framing panels, the whole thing, a bit like how a car manufacturer crash tests a car. They build the whole car, there's no guessing. But with Grenfell, they didn't know that was going to behave like that. But, a full scale test did tell them that's how it would have happened. There were no surprises on what happened there, because they did do full scale testing and generic testing there.
I'm going to play this quick video here, and this is a full scale test, AS 5113. They run for 30 minutes, we'll see it over three minutes. There's three points, at 10 minutes, the heat damage, 14 minute mark and the 17 minute mark.
So on the left, you see a solid aluminium. This is in Australia, CSIRO test facility. The crib is made out of timber, this is basically a duplicate of the British Standard BS 8414, which has been around a long time and it's well respected. That’s been adopted pretty well solidly through Europe as well. Australia took that same test standard. You’re going to see some heat transfer here happening, because solid aluminium is a super heat conductor and it travels, as you can see. On the left the solid aluminium, you can see the heat transfer at the top level of the panels. It transfers heat at 300 times more than Mitsubishi Alpolic, because Alpolic has a non-combustible mineral core. It negates that severe, extreme transfer of temperature. There’s a benefit to composites, they have their places on performance. 14 minutes in, you can see the flame at the top of the rig on the solid aluminium, and behind the panel. You can just see flashes of orange licking at the top of that rig, that's an instant failed. It's failed before it's halfway through this test, that's solid aluminium, 3mm solid aluminium.
More alarming as we get towards the end at 17 minutes, you'll see the solid aluminium sheet at the top at the top of the rig, that panel actually comes loose and falls off. It gets captured by the thermocouple bar, that's a bar that runs horizontally. It's not part of a façade, its part of the test rig. You can see more flames licking at the top of it, that's so alarming for a building. Here we are in 2022 and we're seeing solutions forward like this. That whole panel has come off now. In a real fire in a real city, that's fallen on to the footpath, it’s going to kill someone running out of the building or the fire brigade will be running backwards to avoid it. And that's unacceptable, that’s alarming. The worry with this is that this will cause litigation as it does today, beyond the NCC. There's no defence to say “the NCC just said I had to make this, this is why I use this panel”. it comes back to consumer law where the material or the product needs to be fit for use, fit for purpose, and that will expose you, so AS 5113 will put you in a good place.
Look at the difference, left to right, you tell me which panel is better in a fire. That’s Alpolic NC, composite mineral core, noncombustible on the right, so please don't think that 1530 will put you in a good place.
What we've seen is AS 5113, but let's jump on to this last video and have a look at the global sense. This is Alpolic Mitsubishi in a European video, runs for a minute, but you'll see from this how they engage with this sort of testing from their video. You’ll hear about our BS 8414.
You can view the video here.